Automated part repair using 3D scanning and supersonic 3D deposition
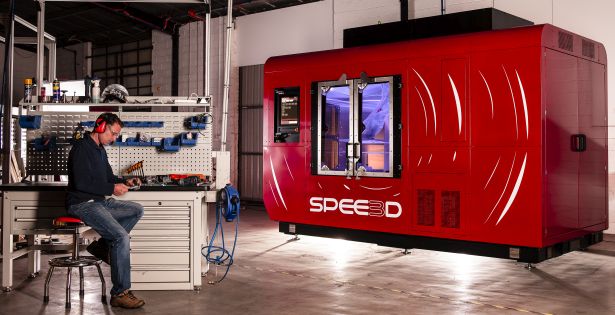
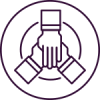
Industry partner
SPEE3D (Effusiontech Pty Ltd)
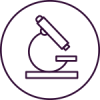
Research organisation
University of Technology Sydney (UTS)
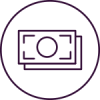
Manufacturing investment
$979,687
($204,551 IMCRC)
for 2019–2020
Simple, fast and customised part repair capability
Challenge
The ability to repair and produce complex objects autonomously in a remote environment is highly sought after by resource and transport companies, and Defence contractors alike. With the release of WarpSPEE3D, SPEE3D’s 2nd generation, high-speed 3D metal printer, repairing larger and heavier components for different industry applications is now possible due to the printer’s larger build volume.
Proposed Solution
SPEE3D is continuing its collaboration with the University of Technology Sydney (UTS) to develop and demonstrate key technologies required to automate and digitalise the repair process for a broad range of Australian and global industry applications.
Building upon SPEE3D’s supersonic 3D deposition technology and the 3D scanning technology developed by UTS as part of the IMCRC project “Machine vision for Industry 4.0 high speed printing”, the project will, in the first instance, focus on upscaling the core technology for the new WarpSPEE3D printer.
Once integrated, the research team will develop core algorithms to determine the necessary paths to allow SPEE3D’s supersonic 3D deposition technology to repair worn or damaged metal components.
The automated part repair capability of the WarpSPEE3D will offer SPEE3D first mover advantage, providing new business opportunities for “repair as a service” and ownership models around the repair equipment.