Application of Additive Metal Technology to Operational Aircraft
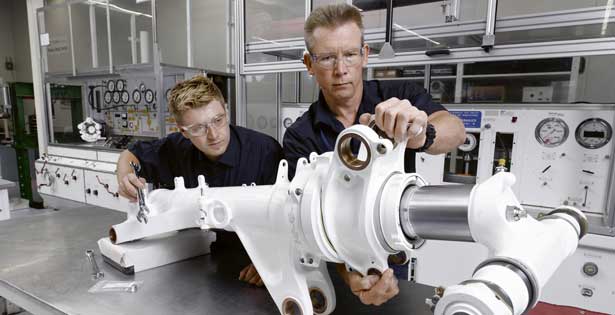
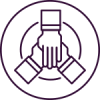
Industry partner
RUAG Australia
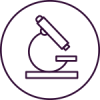
Research organisation
RMIT University
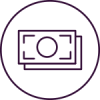
Manufacturing Investment
$1,150,781
($124,809 IMCRC)
for 2018–2020
Additive manufacturing to address metal damage in operational aircraft
Challenge
Metal damage particularly corrosion impact and wear is endemic to operational aircraft. This is currently addressed using a find and fix or a replace approach, where if the damage exceeds a certain size, major repair or part replacement is required. This results in extended aircraft downtime or scrapping of the section.
Proposed Solution
In collaboration with RMIT University, RUAG Australia aims to develop an additive manufacturing process to address metal damage affecting the integrity of components in operational aircraft particularly high strength steel and titanium components.
By exploring geometry restoration via additive metal processes primarily Laser Additive Deposition (LAD), the research teams aims to overcome problems associated with metal structural components without the need for traditional major structural repair or component replacement. In addition, once proven the process would allow parts to be repaired without removal and transport back to a central maintenance facility or replacement parts being built “onsite”. The additive manufacturing technology could be located at the base/hanger where the operator would apply it directly and fix the part whilst still on the aircraft. This is an important outcome for Australia where aircraft needing repair are often remotely based from repair facilities and OEM’s, which reduces revenue and operational readiness.
If successful this project will open the door for RUAG Australia and its partners to extend the technology to address Australia’s and the worlds challenges with metal degradation with a technology that has no serious rival and has already been shown to have potential in this area.