Downer, UTS Rapido and IMCRC celebrate first-year of research alliance
Downer’s Mineral Technologies business and research alliance partners, University of Technology Sydney (UTS) and Innovative Manufacturing CRC (IMCRC) recently celebrated its first year researching solutions that will revolutionise the way mining products are manufactured by using additive manufacturing, or 3D printing as it’s more commonly known.
Alex de Andrade, Associate Professor with UTS and Mineral Technologies Global Manager, Sales, Equipment and Technology said that with one year now completed the team has achieved green lights for all milestones including budget, innovation, collaboration and safety reviews.
“In the first year we have designed a small printer and machinery code as well as printed a scaled version of our selected spiral model. We are now into the cost and wear testing comparisons and in parallel we are building the full-scale bespoke prototype printer”, said Alex.
Hervé Harvard, Director at UTS Rapido and ProtoSpace said: “The project is a world class innovation in the area of Industry 4.0, particularly Additive Manufacturing and IoT sensing, in regard to what the project has achieved. Working with such an innovative team at Mineral Technologies is refreshing and shows that Australia can be a leader in adopting Industry 4.0 principles for global impact,” Hervé says.
Impressed by how well this research project has progressed within its first year, David Chuter, CEO and Managing Director of IMCRC, commented on the positive impact of industry and research organisations working together.
“This is an exceptional project that takes industry-led research collaboration to the next level. Within a year we have seen Mineral Technologies and UTS form a team that “collaborates to innovate” and deliver on their set milestones. Seeing a 3D printed version of their selected spiral model puts it into perspective.”
Marking the progress and the collaborative nature of the project alliance IMCRC has produced a short three-minute video which you can watch by clicking below.
The end goal of the alliance is to allow Mineral Technologies to manufacture bespoke models for mineral separation spirals, sent directly to a 3D printer solution. The commercial benefits include the ability to print on site and in real time which will ultimately deliver savings in both time and money.
“We are excited about the opportunities that our alliance and this particular research project will help to deliver. Beyond commercial benefits are the positive environmental impacts such as decreasing the need for chemicals and reducing air contamination in the manufacturing process,” says Alex.
Another key benefit of the project is the PhD study program which incorporates many students including Thomas Romeijn, a chartered mechanical engineer with Mineral Technologies. To date the research project has completed multiple capstone masters achievements for UTS including winning a 2019 NSW iAwards for a rotational 3D printing system.
Alex says the research team has also confirmed the opportunity for additional development scope around Internet of Things (IoT) connectivity that will deliver the Industry 4.0 milestone outcomes that the project originally set out to investigate, one of which already has a patent pending. This scope growth funding has again been matched by IMCRC.
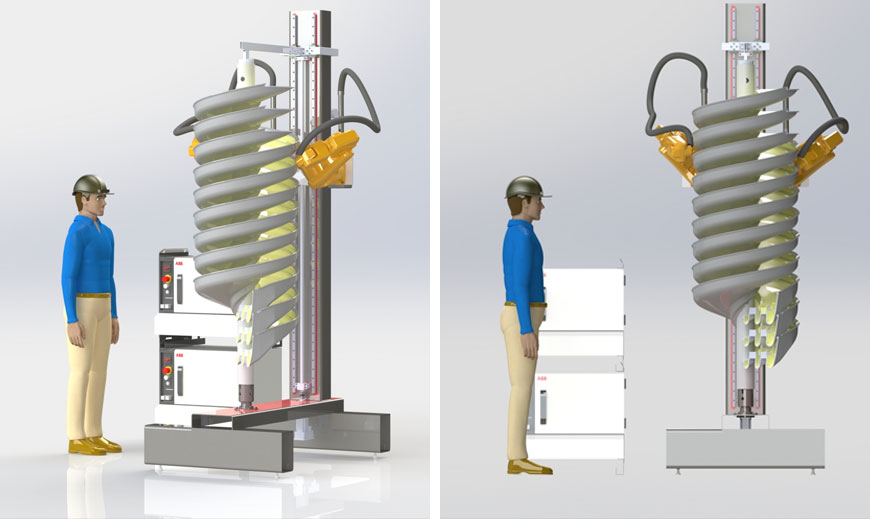