Alloy development for additively manufactured heat exchangers
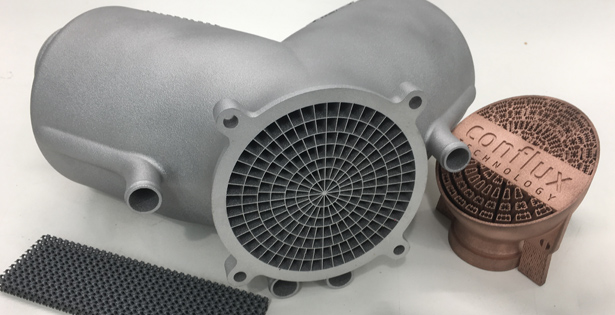
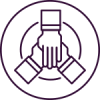
Industry partner
Conflux Technology
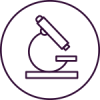
Research organisation
Deakin University
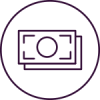
Manufacturing investment
$655,037
($124,456 IMCRC)
for 2022
Improving the performance of heat exchangers
Challenge
Additive manufacturing (AM) enables efficient manufacturing of compact heat exchange devices with highly complex geometries and more efficient use of space than traditionally manufactured heat exchangers. The laser power bed fusion (LPBF) process, as used by Conflux Technology, has revolutionised the design and manufacturing of heat exchangers. Yet, the alloy compositions that are currently commercially available to additively manufacture heat exchangers lack the thermal conductivity properties as their counterparts used in the traditional casting process.
Proposed Solution
In collaboration with Deakin University, Conflux Technology seeks to develop novel aluminium alloys compositions that improve the overall thermal conductivity performance of additively manufactured heat exchangers.
Tapping into Deakin University’s advance material expertise, the project will design several high-performance alloy compositions with high thermal conductivity, good strength and other unique material properties, creating opportunities to optimise the design and geometrics of current heat exchangers. As part of the project, researchers will also determine and validate the best heat treatment procedures for the new alloys.